THE CUSTOMER
Headquartered in California, this brand brings over two decades of expertise crafting premium bed linens. Originally established with a family-owned factory in India, it supplied high-quality bedding to leading global retailers. In 2017, the company shifted to a direct-to-consumer model, focusing on delivering exceptional products at accessible prices.
The brand dedicates its bedding to quality, comfort, and sustainability, designing it to enhance sleep and support environmental responsibility. By combining thoughtful design with a commitment to fair practices, the brand empowers customers to enjoy luxurious, reliable products while making eco-conscious choices for a better future.
THE CHALLENGE
As the brand’s success grew, the company encountered increasing challenges in managing warehouse storage costs and order fulfilment, particularly during seasonal peaks.
They needed a warehousing partner that could handle up to 300 pallets of product, maintain product quality and meet demanding fulfilment requirements. The company also required precise item tracking due to high inventory turnover, product movements between the chosen third-party warehouse, and onward journeys to various distribution centres. Ultimately, the selected warehousing partner’s essential requirements were efficient storage, precise stock management, and streamlined order fulfilment.
Additionally, the need to manage product returns and rework introduced further complexity. Expertise in handling returns and rework operations such as modifying, repairing, or repackaging goods was critical, emphasising quality assurance to ensure operational efficiency and customer satisfaction.
To address these challenges, the company reached out to AMCO. They needed a logistics partner capable of delivering scalable warehousing with an advanced inventory management system and robust fulfilment capabilities.
THE SOLUTION
AMCO developed and implemented a comprehensive logistics and warehousing solution tailored to the customer’s requirements. AMCO’s solution encompassed managing sea freight shipments from India to the UK, handling customs clearance, and coordinating final-mile road transport to AMCO Park, the company’s warehouse facility in Redditch, Worcestershire. The service also included efficient pick, pack, and dispatch operations, robust returns, and rework processes.
DELIVERY—Upon arrival at AMCO Park, warehouse operatives unloaded hundreds of boxed goods out of 40-foot containers, including pillowcases, mattress protectors, and duvet sets, into the warehouse by hand.
SORTING—AMCO Park’s advanced Cardex carousel system efficiently sorts and organises products into predefined categories (A, B, and C) based on demand frequency and product type. This system enables rapid product retrieval, the first step in the pick, pack, and dispatch process.
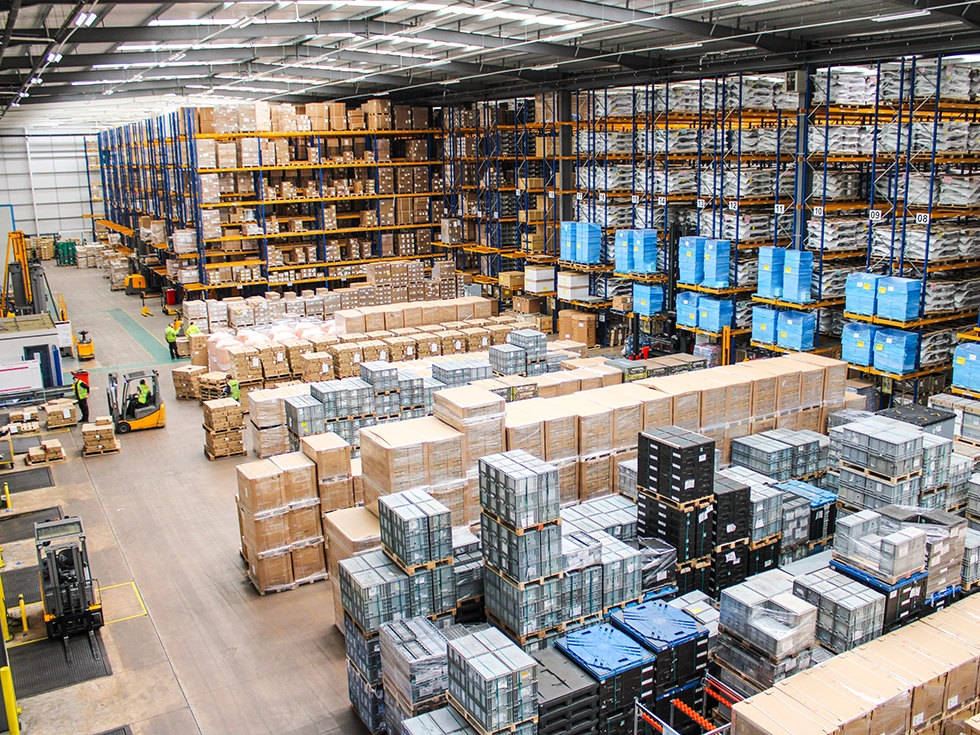
STORAGE—The team sorts the products, palletises and labels them, books them into the WMS, and strategically stores them in the warehouse for product call-off. From here, all product items are accurately tracked and traced via AMCO’s WMS RFI barcode system.
PICK, PACK, & DISPATCH – AMCO’s Cardex carousel system activates immediately upon product call-off, delivering items directly to the warehouse operative’s workstation. This process reduces manual handling and accelerates picking efficiency.
The saved time allows for thorough packing. Orders are manually checked, securely packed, and inspected to ensure quality and customer satisfaction.
Before dispatch, orders are labelled to SSC standards for seamless processing at supply chain distribution centres. This labelling ensures full traceability during transit.
RETURNS & REWORK—AMCO also handles product returns through a robust returns management process. Products undergo a rigorous inspection, relabelling, and repacking process conducted within a clean-room environment to ensure product quality is not compromised.
STOCK MANAGEMENT— AMCO performs regular cycle counts to maintain inventory accuracy, optimise stock levels, and ensure efficient order fulfilment. This process involves routinely counting a portion of inventory instead of conducting a full-scale audit. Cycle counts help quickly identify and resolve stock discrepancies, preventing fulfilment issues and protecting the brand’s reputation.
THE RESULT
AMCO’s solution reduced customer storage costs, enhanced order fulfilment speed, and ensured precise inventory tracking with robust returns management.
Efficient pick, pack, and dispatch operations improved accuracy and quality control. Scalable warehousing and advanced systems optimised stock levels, streamlined processes, and maintained customer satisfaction, empowering the customer’s brand to sustain growth with confidence.
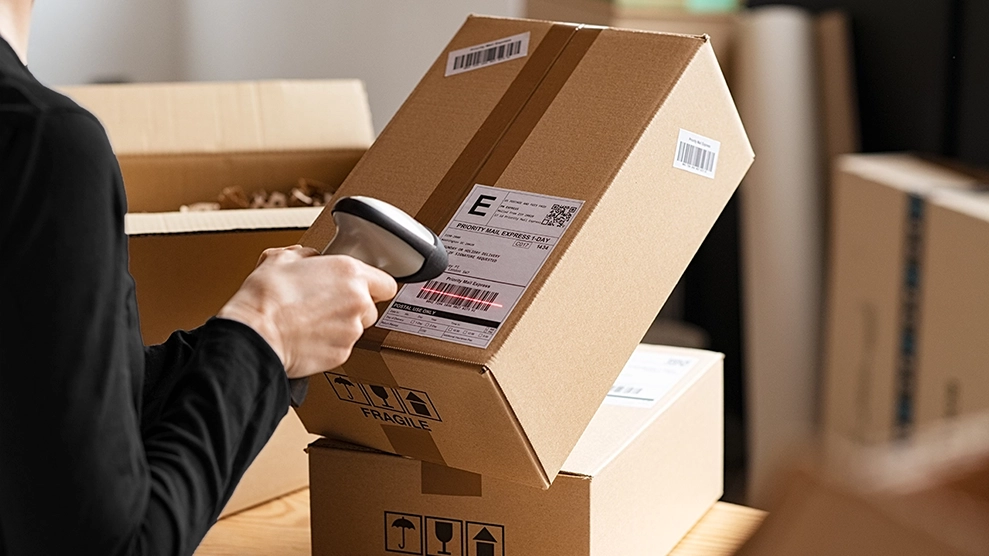
TESTIMONIAL
“Since our partnership began with AMCO in January 2021, we have scaled our business confidently and streamlined operations. It’s enabled us to build our business whilst remaining true to our promise – provide eco-conscious premium bedding at accessible prices.”
Head of Operations, Global Bedding Retailer